聚焦“5G+工业互联网”:技术进步5G赋能钢铁行业
作者:文辉 栏目:要闻资讯 来源:东方财富 发布时间:2021-11-16 03:36 阅读量:17650
钢铁行业属于典型的流程生产行业,生产过程是连续不断的,想要在复杂环境下及时传递大量信息,原有的信息化系统亟待智能化改造。
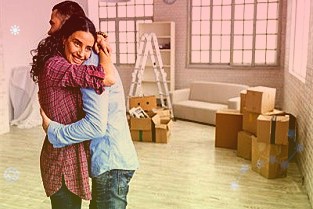
最近几年来,5G+工业互联网以大数据赋能,促进远程操控,协同作业,故障诊断等功能加快应用,正助推这一传统行业提质增效。
过去,操作工在生产车间里挥汗如雨,如今,坐在操作室就能远程操控生产过去,生产设备如果发生故障,影响产品质量,一般到最后抽检才能发现,如今,传感器自动监测设备运行,实时诊断故障并精准定位,良品率更高了
钢铁行业的生产场景相对复杂,生产工艺要求较高最近几年来,得益于5G+工业互联网的推广和赋能,钢铁生产制造逐渐向数字化,智能化方向转型,技术的进步为行业高质量发展带来了更多动力
远程操控
生产更安全高效
巨大的电磁吊具,吸附起数吨重的废旧钢材,提升,横移,调整位置,再精准地放置到运输车斗里在湖南华菱湘潭钢铁有限公司的5米宽厚板厂炼钢区,4台天车正紧张有序作业
此时,操作工谭彬正坐在宽敞的远程操控室里,目视屏幕,拨动摇杆,按动按钮,轻松完成装载吊卸任务以前在天车桥架下的操作室里工作可不是这样的粉尘多,噪音大,虽然操作室里已经相对封闭,但时间长了,还会有灰尘漫进来,工作时必须时刻戴着口罩
帮助谭彬实现作业环境改变的,是华菱湘钢利用5G+工业互联网技术实现的天车智慧改造项目。越来越多的钢铁企业受到影响。各厂可能会陆续实施,整体开工率会再次下降。
华菱湘钢生产设备部副部长何炜介绍,利用新技术的超高可靠性与超低时延,车间实现了数据的超高速上传与下载,能对设备进行精准化操控,真正实现人与机器的分离5G+天车的智慧化改造,让工人的效率提升了不少
在宝钢股份湛江钢铁有限公司热轧厂,工作人员吴耀腾有同样的感受说起5G技术给工作带来的变化,他连连点赞:现在坐在办公室里就能远程操作设备,安全舒适还高效!吴耀腾负责车间内无人天车的运行跟踪,以前他要在10多米高的天车上操控机器,精神必须高度集中自从应用新技术后,无人天车帮了大忙,少了上下车的危险,而且一个人就可以控制4台天车
5G+智慧钢铁的场景应用已多点开花,类似5G天车远程控制,自动控制等,已具备大规模复制的技术和产业基础中国移动广东公司湛江分公司总经理潘卫东表示,未来,5G结合人工智能和云计算等技术,能帮助解决钢企网络碎片化和信息孤岛的问题,并在制造和管理中引入信息化,数字化和自动化解决方案,提高企业的生产效率和盈利能力
协同作业
机器实现默契配合
在钢铁生产车间,推焦车,拦焦车和熄焦车呈一条直线排列,行驶到炭化室后,即将进入推焦,拦焦,熄焦等工序在推焦过程中,机车自动识别所处炉号,并行驶到对应炉号旁记者最近几天在河北唐山的首钢京唐公司看到,整个过程如行云流水般自动完成
对钢铁企业来说,焦炉是不可或缺的设备焦炉的四大机车——推焦机,拦焦车,熄焦车,装煤车,分工不同,又相互联系,通过信号的传送构成有机统一的整体
在中控室的显示器上,四大机车的运行数据一目了然整个管理系统除了可以实时监测机车运行情况,还能实现人机对话,发送工作指令焦炉四大机车运行数据由设备本体集中上传到中控室,过去由于带宽小,图像传输常常出现卡顿,滞后京唐公司焦化部生产室工作人员丁洪旗介绍
钢铁行业属于典型的流程生产行业,生产过程是连续不断的,想要在复杂环境下及时传递大量信息,原来的信息化系统已经难以为继,对智能化制造需求迫切2019年,京唐公司焦化部将5G技术应用于四大机车的远程操作中,实现多机智能化同步联动,使设备远程操作模式更加可靠,高效,安全
我们现在实现了图像的稳定,安全,快速传输,中控室经过分析,逻辑判断后,发出相应指令到机车的可编程逻辑控制器,从而实现四大机车的分工合作丁洪旗说
华为5G钢铁行业专家彭俊说,相比其他无线制式,5G的优势更突出,可以将生产现场的多台设备按需灵活组成一个协同工作体系,实现分工合作,提高生产效率,降低生产能耗据介绍,自2019年以来,首钢京唐公司利用5G+工业互联网等技术,推动钢铁制造技术与装备转型升级,生产效率提升了约15%
故障诊断
实时监测主动维护
伴伴随着轰隆隆的响声,红彤彤的钢板在滚轮上快速移动,经过轧制,喷淋冷却变成黑色的钢带,再卷曲成钢卷在辽宁鞍山的鞍钢股份热轧带钢厂,1780热连轧生产线生产作业区作业长马良在后台盯着显示屏,查看钢带生产情况
马良说,在100多米的传输轨道上,一共有400多个辊道,在热轧过程中,如果某一电机出现故障使得辊道停滞,就会造成钢带表面的大面积划痕,影响产品质量以往这类问题只有在产品最后抽检时才会发现,但等发现时生产线上可能已经又生产出好多有划痕的产品了
2019年,鞍钢在1780热连轧生产线建设5G+设备预测性维护试点,有效解决了这一问题鞍钢信息产业公司首席研究员刘佳伟介绍,利用‘5G+工业互联网’升级关键基础设备后,设备传感器收集的温度,振动,压力,流量等数据,会实时传送到云端,再通过人工智能和大数据分析,就能实现即时的监测,诊断,处置等
以1780热连轧生产线为例,应用5G+工业互联网后,每个辊道的电机电流都会被实时采集,一旦出现异常就会立刻报警并精准定位以前发现产品划痕后倒查问题,需要对400多个辊道逐一排查,要花半个小时到1个小时不等,现在10分钟内基本就能确定问题
除了故障维修外,5G+工业互联网的应用还实现了对设备的主动维护。数据显示,根据唐山调坯型钢企业反馈,轧钢企业自9月27日0时起停产,吊装时间待定。据不完全统计,9月份,全国多个省份发布了钢铁企业停产检修情况,涉及80多家钢厂。数据显示,广东,广西电炉钢企平均开工率不足50%,浙江多家电炉,轧钢厂被迫停产,而山东近几天减产的钢企数量仍在增加。。
以往维护设备主要靠人员进行点检定修,现场工作量大,有危险性,而且准确率不高有些设备的备件状态还正常,但到了更换周期就要更换,造成了浪费,有些备件已经有劣化趋势,点检时没发现,就可能发展成故障这些都高度依赖点检人员的经验刘佳伟说,现在,老师傅的经验转化为数据模型,通过数据分析,科学维护设备,实现对设备的全生命周期管理在1780热连轧生产线上,改造后的紧急停机,故障维修次数下降了20%,机组作业率提升了5%
。郑重声明:此文内容为本网站转载企业宣传资讯,目的在于传播更多信息,与本站立场无关。仅供读者参考,并请自行核实相关内容。
内容摘选
